In the rapidly evolving manufacturing landscape, where cutting-edge technologies like AI, robotics, and IoT dominate discussions, it may seem counterintuitive to focus on obsolete technologies. However, maintaining a workforce trained in these older technologies is crucial for several strategic reasons. From ensuring smooth transitions during upgrades to preserving valuable industry knowledge, the benefits of such training can significantly impact operational continuity and competitive advantage.
This article explores the importance of keeping workers trained on obsolete technologies in manufacturing, outlining the multifaceted benefits and providing insights into how companies can effectively manage this process.
Ensuring Operational Continuity
One of the primary reasons to train workers on obsolete technologies is to ensure operational continuity. Many manufacturing plants operate machinery and systems that are considered technologically outdated but are still critical to production due to specific capabilities or cost-related reasons. Until these technologies can be upgraded or replaced, companies must maintain their functionality.
Training new employees on these older systems is essential because, without knowledgeable operators, the risk of downtime increases. Downtime in manufacturing can lead to significant losses in productivity and revenue, making it imperative to have skilled personnel capable of managing and troubleshooting older technologies.
Preserving Institutional Knowledge
Obsolete technologies often carry with them a wealth of institutional knowledge that can be invaluable, especially in custom or niche manufacturing operations where specific processes and machinery are tailored to unique product requirements. As experienced workers retire or move on, they take with them critical operational insights that are not easily replaced by simply hiring new staff.
By training new employees on these older systems, companies ensure that this knowledge is preserved and passed down through generations. This not only helps in maintaining the quality and efficiency of current operations but also serves as a treasure trove of information that can inspire innovations and improvements in future technologies.
Facilitating Smoother Technology Transitions
Upgrading to new technologies is not an overnight process and often happens in stages. During these transition periods, parts of the manufacturing process may still rely on older technologies, like legacy servo motors, while others shift to newer systems. Training workers on both sets of technologies ensures that they can operate across different platforms, facilitating smoother transitions and reducing the risk of errors or inefficiencies that can occur when systems are incompatible.
Moreover, workers who understand the functionalities and limitations of obsolete technologies can provide valuable insights into how new systems can be designed or modified to better meet production needs. Their hands-on experience with older systems makes them excellent resources for identifying potential issues and suggesting practical solutions during upgrades.
Leveraging Cost-Effectiveness
Replacing industrial machinery and systems involves significant capital investment, and it’s not always immediately feasible for many companies, especially small to medium-sized enterprises even if they have proper sourcing partners. Maintaining and effectively operating existing, albeit obsolete, technology is often more cost-effective in the short to medium term. Training workers to proficiently handle these older systems ensures that they continue to deliver value, maximizing the return on the original investment until resources can be allocated for upgrades.
Building a Versatile and Resilient Workforce
Training workers on a variety of technologies, including obsolete ones, contribute to creating a more versatile and resilient workforce. Such training enhances problem-solving skills and adaptability, qualities that are invaluable in a sector as dynamic as manufacturing. Workers who are comfortable navigating both old and new technologies are better prepared to handle unexpected challenges and can significantly contribute to the agility of the manufacturing operation.
Strategies for Effective Training on Obsolete Technologies
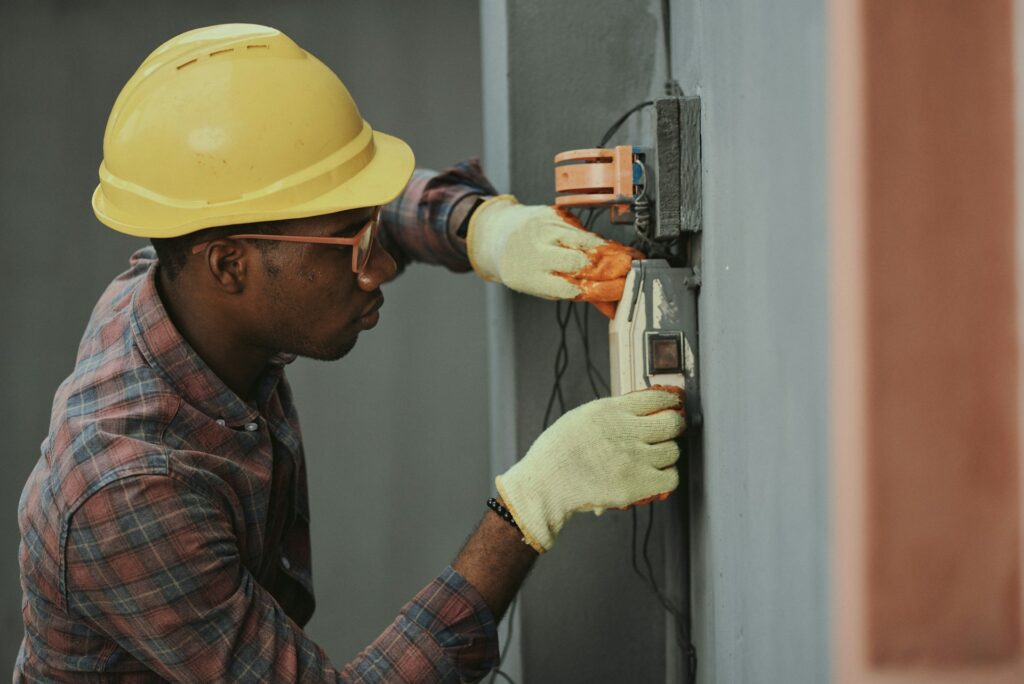
- Develop Comprehensive Training Programs: Create detailed training programs that cover both the theoretical and practical aspects of obsolete technologies. Include manuals, hands-on sessions, and mentorship programs where experienced workers can pass down their knowledge to newer employees.
- Incorporate Regular Updates and Refresher Courses: Technology, even obsolete, can undergo minor updates or changes. Regular training sessions ensure that workers stay updated on any changes and refresh their skills on the equipment.
- Foster a Culture of Learning: Encourage a workplace culture that values continuous learning and knowledge sharing. This can be facilitated through workshops, seminars, and cross-departmental initiatives that highlight the importance of understanding all aspects of the manufacturing process, old and new.
- Utilize Technology Simulations: Where possible, use simulations and virtual reality (VR) tools to train workers on obsolete technologies without the need for actual machine time. This can reduce training costs and minimize the risk of errors during the learning process.
Conclusion
While it may appear counterproductive at first glance, training workers on obsolete technologies hold significant strategic value in manufacturing. It ensures operational continuity, preserves invaluable institutional knowledge, facilitates smoother transitions during technological upgrades, and contributes to cost efficiency.
By investing in comprehensive training programs and fostering a culture of learning, manufacturers can turn what seems like a liability into a potent asset that not only supports current operations but also paves the way for future innovations and success.